11 Ways Your Machine Shop can Optimize Performance
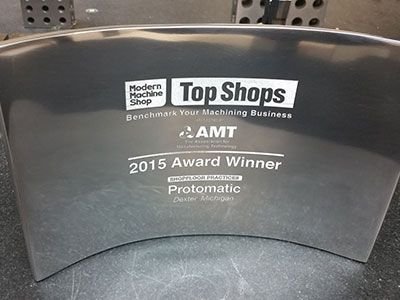
For the past 5 years, Modern Machine Shop Magazine has published its “Top Shops” issue where it highlights the best practices of top performing machine shops from a broad survey of the U.S. machining industry. This year, Protomatic was recognized as a “Top Shop” for our Shopfloor Practices. Others were recognized for Machining Technology, Business Strategies and Human Resources.
It’s no surprise that leading shops are committed to investing in great equipment, getting capable people, staying close to their customers, and managing operational details to get the highest levels of quality and productivity. This is the tried and true way to do well in most businesses. But the machining business is more challenging than most businesses. It relies heavily on expensive capital equipment containing rapidly changing technology, and technically savvy professionals. And that’s just the start.
Owners and managers seem to have done a pretty good job of optimizing their costs, quality, and delivery to fit their customer segments. As a result, the low hanging fruit in machine shops has largely been picked.
Given this, in order to improve, organizations are required to be increasingly creative in finding ways of optimizing performance. The first challenge is to identify viable improvement opportunities. The next challenge is to develop a solution to get the actual improvement. This is then followed by the implementation of the solution. Making all this happen requires a lot of effort.
Einstein had it right when he said, “A problem cannot be solved at the level at which it was created.” He was arguing for a changes in perspective and scope in defining problems and identifying the solutions. A few approaches that have worked for Protomatic, and can be used as guidelines for other organizations, include:
- Get creative by changing perspective. Look at the big picture.
- Never place limits on your thinking.
- Look to the customer. What do they value and pay for?
- Add people with different knowledge and experience to the conversation.
- Challenge beliefs about the business.
- Dissect the business and experiment with new combinations.
- Be systematic. Use formal innovation and problem solving tools.
- Ask what we can ADD? ELIMINATE? REDUCE? SUBSTITUTE? SEPARATE? INTEGRATE? RE-USE? STANDARDIZE?
- Measure inputs, outputs, and performance.
- Identify the most important measures.
- Recognize that the best opportunities announce themselves with ambiguity and conflict.
This is only a beginning. There is a huge body of knowledge on innovation, improvement and the like. Most of the tools can be helpful. Recognize the potential value these approaches can have to the business. Talk to the team and let them know what is being done and why. Start moving and don’t quit. Ever. Over time the improvements will build up and success will be guaranteed.
Adhering to these guidelines and making them the foundation for our quality standard of “life-saving precision” is what propelled Protomatic to being named a “Top Shop.” To learn more about what to look for in a premier machine shop, download the FREE eBook, “Tips for Choosing a Prototyping Machine Shop.”
About the author: Doug Wetzel is Vice President and General Manager of Protomatic. Protomatic is a CNC precision machining shop specializing in prototype and short-run production components for the medical, aerospace and other technical industries. Because of the critical nature of the parts they design and manufacture, the emphasis is always on Life-Saving Precision.