All aluminum isn't the same. What grade is best for you?
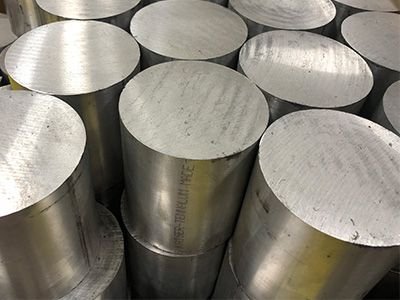
Aluminum is one of the most universal materials and is widely used in many CNC machining applications. It is cost effective, easy to manufacture with many methods, has a good strength to weight ratio, and is naturally long lasting with low corrosion rates.
If aluminum is the best choice for your application, then some alloy fine tuning is available to the designing engineer. The following is a knowledge base for aluminum comparison and is provided by Protomatic as a guideline.
Temper
If your application is subject to physical stresses, the design may be focused on the aluminum heat treating, also called temper. This heat treat process changes the tension yield strength — a measurement of the linear stretching strength of the material. The “ultimate strength” is the strength measured to the point of failure/break. Both are measured in KSI, which is thousands of pounds per square inch of material (English units).
Elongation
The second important property is called “elongation.” Elongation is a measurement of the percentage of stretch before a test sample failures or breaks. Materials are typically stronger for tension yield strength when heat treated but are more brittle. Brittle material will have a low elongation percentage. As an example, a rubber band will have a very high elongation percentage. Many metals are in the 6%-45% elongation range. Ceramics will be 0-1% typically, while plastics and rubbers could have greater than 100% elongation values.
Alloys
Alloys are designed for manufacturability and application. Billet alloys are slightly different from casting alloys. Billet manufacturing may be a forging, rolled or extrusion-based process. Typically, these are higher strength due to the manufacturing method. Castings are a poured or injected process, usually utilizing a liquid metal. A casting process may create porosity from moisture or gases trapped in the part when cooled. This porosity produces a lower strength part and must be considered in the design for optimization.
The following tables demonstrate the differences for billet and cast aluminum.
Common Aluminum Alloys – Billet
Common Aluminum Alloy – Casting
Of course, material selection is more complex than simply tables, because each application has other considerations, such as temperature of service for the part, shock, creep, fatigue, surface finish, cosmetic requirements, etc.
If you have any questions or need to prototype a few design variations to validate testing, please contact Doug Wetzel at Protomatic at Doug@protomatic.com or our sales team at Sales@protomatic.com.
Protomatic is the precision CNC manufacturer with extensive experience working with aluminum, as well as other materials including superalloys, titanium, plastics, rubber, composites and refractory materials.
About the author: Doug Wetzel is Vice President and General Manager of Protomatic. Protomatic is a CNC precision machining shop specializing in prototype and short-run production components for the medical, aerospace and other technical industries. Because of the critical nature of the parts they design and manufacture, the emphasis is always on Life-Saving Precision.