Appearance is Everything
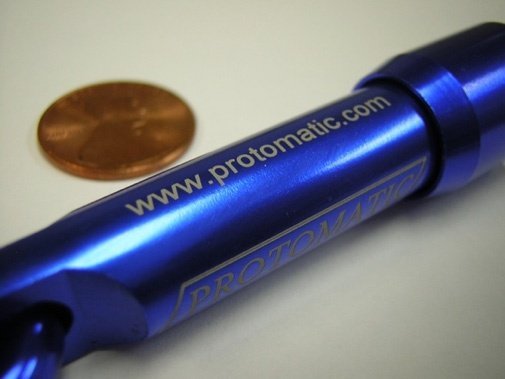
Cosmetics matter. Many of our customers look well beyond the dimensional performance of the part. They are concerned with their image and the quality of finish that is on the part. Cosmetics make the difference in the look and feel of the part. This month we are highlighting some of the specialized finishes that are available at Protomatic that can differentiate your product from your competition.
Machined Surface
Machining metal and plastic creates unique marks that identify the method of manufacture. But, sometimes these marks are not desireable. The measurement of the surface roughness in layman’s terms is the average amplitude in microinches of the surface. A typical milling operation produce finishes in the Ra 32 (Root means squared average microinches of amplitude) to Ra 64 range. A highly lapped or polished surface would be Ra 2. By varing the feed rate, cutter technology and coolant used, Protomatic has achived a surface finish as machined in the Ra 4 to 6 range. This can remove secondary operations such as lapping or polishing.
Sanded Finish
Another way that Protomatic changes the finish is simply a fine sanding. This can be done to almost all materials. With various grits of sand paper. A 240 grit paper produces a coarse finish, 320 grit a medium, 600 grit paper produces a fine, 1500 grit is ready for polish.
Textured Surface
If a uniform matte finish is desired. Glass Bead blasting is an inexpensive option. Tumbling with abrasive media or electrochemical processes are posible.
Polished Finish
Polishing is accomplished by machining, and sucessive sanding operations. Polishing compounds typcially utilize one of four common medias: aluminum oxide, silicon carbide, sapphire or diamond. These abrasives are commonly suspended in a lubricating solution such as water, oil, grease or wax.
Anodize and Passivation
Common surface stablization methods are anodize and passivation. Anodize is basically a controlled corrosion with an impregnated dye and seal. Passivation is an acid etch typcially used on stainess steel to create high surface chromium to prevent long-term rust.
Plating
There are hundreds of different plating processes available. Some of the more common are: Zinc, phosphate, black oxide, electro-less nickel, chrome, cadmium, tin, lead, silver, and gold.
Coatings and Paints
Dry Film Lubricants and CARC paints are also common. Powder Coat, and E-Coat are also available. These coatings are very tough and provide reliable and long term coatings that are perfect for most applications.