Best Practices for a CNC machining shop aren’t good enough.
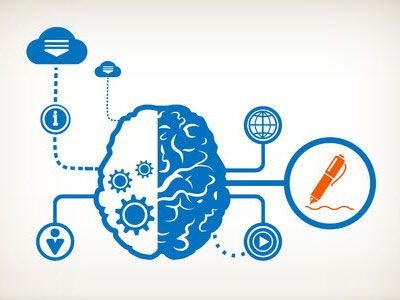
The implementation of Best Practices is something we have all been taught to strive for. And with good reason. But for a CNC machining shop, we really need to go a step further.
But first, let’s take a step back.
Let’s begin with Quality Management Systems (QMS). There’s no doubt that ISO-9001, AS-9001 and ISO-13485 are great for a global view of a corporate operation. A basic QMS also works well when implementing Best Practices for a CNC machining shop. However, whether you have a small or a large business, the details make all the difference between success and failure. In that regard, QMS is only a start.
After 15 years of using ISO QMS, I’ve found they do have weaknesses. For instance, they are definitely lacking in how they address finance, marketing and sales. They also can fall short in helping to develop a strong preventative environment.
A Preventative Environment is the next step.
A QMS is great, but a preventative environment is needed to make that QMS really effective. One good way to improve your QMS is by creating a preventative environment using Process Failure Effect Mode Analysis (PFEMA) methods. They are well described in ISO systems.
Using PFEMA, we created a preventative environment:
- Raising hiring standards
- Better training of personnel
- Automating processes through updated software
- Utilizing a detailed control plan.
Creating a knowledge base is step two.
Of course, how a PFEMA is used will vary from industry to industry. Here is what Protomatic did to create a preventative environment.
Because it is critical to get the most valuable and germane information to employees, we created an instruction-based document to help machinists adhere to “Best Practices” when running CNC milling and turning equipment.
The document is designed to detail all of the various techniques required to meet standard workmanship guidelines. What we found is that while the guidelines are great in defining the “pass or fail” criteria, they don’t provide a clue as to how to accomplish that task. So the instruction-based document Protomatic developed is a “living document” that is modified whenever a new piece of equipment or technique is discovered. The result? “Best Practices” are made even better by regular updating.
Final step — moving Best Practice to Standard Practice
The Protomatic document was initially called “Best Practices for the Machinists.” However, we quickly saw that the logic of the machinist is: “Well, that’s a good way of doing things, but I like my way better.” So our document was morphed to “Standard Practice – INS2203.”
It included all of the little technical tidbits that the senior mechanists had acquired over the years such as: the best way to mount a machinist vice on a mill table; or, to prevent long-term CAT40 taper swelling, the torque required when installing a pull stud on a CAT40 tool holder is 76 ft. lbs. As you can tell, all of the job functions are very detailed.
ISO Quality Management Systems don’t require this type of information to be documented, but we found that these Standard Practices help eliminate manufacturing variations and minimize possible modes of failures as outlined in the PFEMA guidelines. This plays a major role in a preventative environment, and helps Protomatic make parts with life-saving precision.