Dryfilm - Micro Blasting - Tumbling
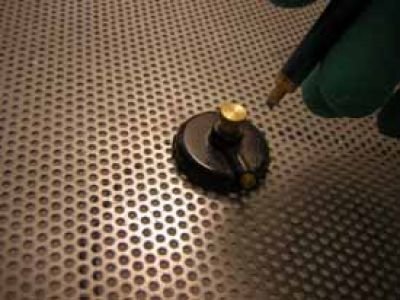
This is the new newsletter for Protomatic Inc.
In working with all of our customers, we sometimes neglect to inform you as to what is new with Protomatic. This information is important in the constantly shifting market and changing market needs.
The following highlights some of the new processes that are now available at Protomatic, which will better satisfy the needs and expectations of our customers.
Dry Film Lubrication Process- AS 5272
For the Aerospace industry, Protomatic recently added the process of Dry Film Lubication coating. This process and material are certified to Mil-L-45010 and AS5272 requirements and are compatible for both Type 1 and Type 2 applications.
Dry Film Lubricant Coatings start out as a high performance paint-like material consisting of fine particles of lubricating pigment such as Molybdenum Disulfide (MoS2), PTFE and Graphite along with solvent, a binder, and other additives to add corrosion protection. Upon application and curing, the solvents are driven off and the lubricant bonds to the surface of the part to form a solid film. This bonded film greatly reduces the coefficient of friction of the surface and increases wear life.
Some coatings are specifically blended to prevent galling. Others are designed to operate at extreme temperatures.
The final dry film thickness of most Dry Film Lubricant Coatings is .0002″-.0005″. They exhibit a coefficient of friction of .02-.08 and can operate under loads up to 250,000 psi. These numbers will vary by the coating of choice and the substrate to which they are applied.
Specific formulations procedures have been developed to allow these coatings to be applied to a variety of substrates including but not limited to:
Steel, Aluminum, Brass, Copper, Nickel, Zinc, Chromium, Stainless, Glass, Rubber,Plastic and Wood.
The typical color of these coatings is gray to black.
Micro Abrasive Blasting
To compliment the products that need to be micro deburred, prepped for Flouresent Pentrant Inpected (FPI) or Magnetic Particle Inspection (MPI), we ‘ve introduced micro abrasive blasting. This is great for small parts that require microfine blast media. This new process gives Protomatic the ablity to control the process for the best finish possible.
Tumbling
Although many companies tumble, we found that the production tumbler’s do not control the tumble process sufficiently enough for Class A surfaces. Protomatic recently installed multiple (3) tumbling machines specifically to tumble only certain alloys of Aluminum. The tumbling machines are not cross contaminated with other metal such as steel, brass, titanum or stainless steel. This, along with additional controls creates a consistent finish on all of the critical secondary operations such as Anodize Type II (Standard Anodize), or Type III (Hardcoat Anodize).