How Does CNC Turning Equipment Size Up?
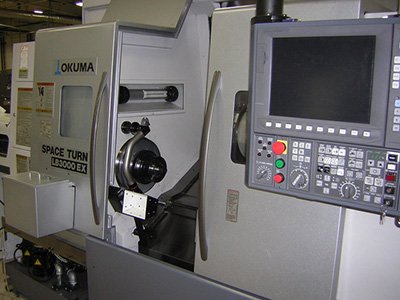
At Protomatic, selecting a CNC milling machine or a turning machine for your application isn’t a snap decision. To help explain our decision-making process, last month we reviewed CNC mill sizes and when a milling machine is the right choice. This article will focus on when a CNC turning machine should be recommended.
Turning or Milling
For starters, Turning is different due to the nature of the operation. In turning operations, the part spins (turns) and the tool is stationary. Milling is just the opposite –— the part is stationary and the tool spins.
Due to this fundamental change, in Turning operations part symmetry is critical to minimize centrifugal (spinning) unbalance. An unbalanced part may create vibration or harmonics from the simple act of spinning the part. This can result in a poor surface finish, or out-of-round conditions on parts.
On the other side, Turning has significant performance advantages to Milling.
• Turning is capable of very high material removal rates. Lathes historically have more horsepower and torque compared to milling.
• A Turning tool is typically in continuous contact with the part. A Milling endmill is only in contact on a portion of each rotation.
• Turning can provide almost polished surface finishes. Milling creates a cutting impact strike with each cutting rotation, reducing the ability to provide ultra-smooth surface finishes.
• Turning has the ability to make very round and concentric parts. Milling operations are limited to boring or circular interpolation, which can have increased error in roundness and concentricity.
Three factors go into machine selection
• Size
Lathe size limits are easy to understand. A given machine has a diameter and a length. Work and tools are limited to that space. A small lathe may have a 6’’ diameter and a 15’’ length. This allows manufacturing of a part up to 6’’ diameter and 15’’ long for outside dimensions. If drilling or boring is required, the length value is halved — limited to about 7’’ long for a part due to 7.5’’- long drilling/boring tool movement required for clearance around the part.
• Complexity and Accuracy
Complex and high-accuracy parts are easily supported with most Turning equipment. At Protomatic, we have simple 2-axis lathes, with up to 8-axis mill/turning equipment. They allow for dimensional relationships requiring precise angles, squareness, parallelism, and orthogonally or collinear relationships in a single operation; and are instrumental in reducing error that may be compounded with multiple setups.
• Productivity
Productivity is more significant with a lathe. The main reason is that the larger the lathe, the lower the maximum RPM available. In Machining operations, the material removal rates are based on material (alloy and hardness) and tool capability. This removal rate is based on a lookup table and is rated in a unit called SFM (Surface Footage per Minute). To produce a constant SFM, the cutting speed for a Turning operation is the same based on adjusting the RPM of the cut as related to the diameter of the cut.
Productivity comes in many forms, but the principle here is maximizing the SFM material removal rate during the cut time. For a small part — typically less than 3’’ in diameter — a large lathe with a maximum RPM of 1000 will be about four times slower than a small lathe with a maximum RPM of 4000. That is based on material removal. Interestingly, CNC Milling equipment does not have this limitation.
What are our sizes?
• Our smallest lathe
Hardinge Cobra T42, Conquest T42
6″ Chuck, 1 5/8″-42mm Thru hole
Size: 9″ ODx 13″ L
Max RPM: 4500-5000
Barfeed: None
2 Axis
• Mid-size lathe
Tsugami TMA8, Mazak QTN-200MY
8″ Chuck, 2.5″- Thru Hole
Size: 8.5-14″ OD x 20-22″ L
Max RPM: Various 3500-10,000
Barfeed: S2-65, S2-80
2, 3, 8 Axis
• Larger lathe
Okuma LB3000-EX-MYW
10″ Chuck, 3″ Thru Hole
Size: 13″ OD x 31″ L
RPM: 4200
Barfeed: S-85
3,4 Axis
This is a very simplified overview of the selection process that is required at Protomatic, and provides insight into our commitment to Life-Saving Precision in every component we manufacture.
Please contact us directly for further assistance or questions.
Scott Allen, Sales Manager Scotta@protomatic.com
Lori Frantz, Sales Lori@protomatic.com
Doug Wetzel, VP/GM Doug@protomatic.com
Brian Heldt, Program Manager Bheldt@protomatic.com
About the author: Doug Wetzel is Vice President and General Manager of Protomatic. Protomatic is a CNC precision machining shop specializing in prototype and short-run production components for the medical, aerospace, and other technical industries. Because of the critical nature of the parts they design and manufacture, the emphasis is always on Life-Saving Precision.