Machining with Carbon Dioxide Coolant
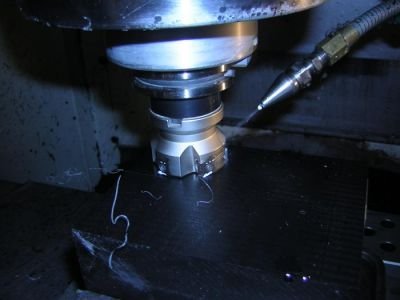
This month we would like to share with all our customers a specialty machining process that is available at Protomatic.
This process is an alternate to the conventional “Flood Coolant” process, which uses an oil and water mixture that is recirculated in the milling or turning center. In many applications, this process works very well due to the cooling and lubricating properties of the water and oil.
However, there are applications where high cleanliness or high performance machining is required. Some highly critical applications, such as high voltage plastic components, medical implanted parts (class 3), low thermal conductive plastics or post adhesive bonding applications, require a non-contaminating process. For these applications, Carbon Dioxide coolant is a great alternative. Below is a mini case study of one application.
Green Machining
Figures 1 and 2 show an example of Carbon Dioxide (Co2) coolant. A block of co-polymer (Acetel) Delrin 150 is machined with a 2” shell mill. The Co2 is contained in a gas/liquid tank at 750-800 PSI and is assisted with filtered, dried shop air at 120 PSI. The combination produces a cool high pressure directional coolant that produces improved lubrication and chip extraction at the cutting edge.
Performance Comparison
The two photos to the left represent a carbide tooling set-up that had an 80% increase in insert life. One can compare the two cooling processes by examining the black lines that mark the extent of the wear pattern in figures 3 and 4.
Additional Advantages
Some of the other advantages include the following:
- Green Solution that is environmentally friendly. (ISO-14000 compatible)
- No Contact with Oil or Water (Water expands most plastics, Oils saturate the plastic surface)
- Removes need for Coolant Biocides and Fungicides
- Living bacterial and fungal contaminants are not in contact with the part (Bacterial growth is common in oil/water coolants).
- Increased tool life.
- Absence of metal contaminants normally present in oil/water coolant (“Micro Fines” that are present in the recirculated coolant can impregnate the part with metal particles.)
- Removes the cost of reprocessing the used oil/water coolant.
- Increased tool life and, in some applications, improved machining finishes. In this case, we witnessed an 80% increase in tool life, significantly reducing insert tool costs.
For more information Contact
Gary Rodak
gary.rodak@machiningefficiencies.com
MachiningEfficiencies.com