Moving into Digital Manufacturing
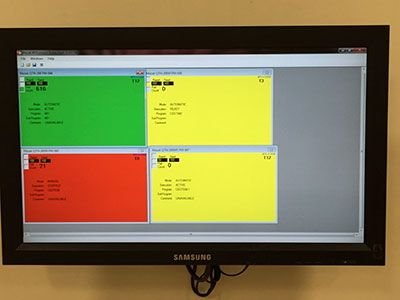
Digital manufacturing requires analysis of data from a diverse set of industrial equipment on the factory floor. Uniform, robust communications are part of the necessary infrastructure for modern business systems and 21st century decision-making. With this in mind, Protomatic is working with MT Connect® to monitor its machines in real time. MT Connect is a CNC machine open-format communication protocol developed by the Association for Manufacturing Technology (AMT), a non-profit organization. This open source license provides the basic tools that retrieve uniform data from CNC equipment, allowing for real-time updates on productivity.
How does MT Connect work?
MT Connect is a common industry communication method that can be adapted to a variety of industrial equipment on the factory floor, using standard Ethernet connectivity. The data is accessible via a web browser or collected with a client application, typically presented as a dashboard-style report. Some client applications store the data in a database to measure trends and collect long-term data.
Purpose:
The purpose is to create more efficient operations with improved production optimization and increased productivity. This is done by providing CNC machine status information to more than just the operator. This is available on the network for operators, programmers, setup machinists, maintenance personnel, repair personnel, supervisors and management.
Information collected:
The CNC machine state is updated in (almost) real time, and the data is provided to the client application. At Protomatic, we display color-coded machine status information for the lathe department, shown below. The type of information is related the machine attributes, spindle speed, feed rate, tool number, error code if in a fault condition, part counters, and status information from the “andon lights”.
Examples of the machine status:
- Green is running 100%
- Yellow is not optimized (feed rate reduced to 50%)
- Orange is halted (part complete)
- Red (Not Shown) is off or E-Stop
Why are we doing this?
Empowerment Management – we want an empowerment workforce. Employees need to know what is going on so that they have the most immediate control of the CNC equipment. Additionally, support personnel, such as the setup or programmer machinist, can observe and recognize the manufacturing status of the job and help the operator if they are having problems with a task.
Job Scheduling – This helps manufacturing management improve job scheduling with monitoring, and is critical for remote access for lights-out manufacturing applications. The machine maintenance group also receives real-time updates of the machine status, and if a machine breakdown occurs, CNC error codes are available and they can respond appropriately. This is a big plus because everyone knows what is going on and can focus on success.
These are just some of the benefits of the MT Connect program at Protomatic. We are working to connect more machines in the future, in our effort to continually provide “Life-Saving Precision” to our customers.
About the author: Doug Wetzel is Vice President and General Manager of Protomatic. Protomatic is a CNC precision machining shop specializing in prototype and short-run production components for the medical, aerospace and other technical industries. Because of the critical nature of the parts they design and manufacture, the emphasis is always on Life-Saving Precision.