Plastic Prescription
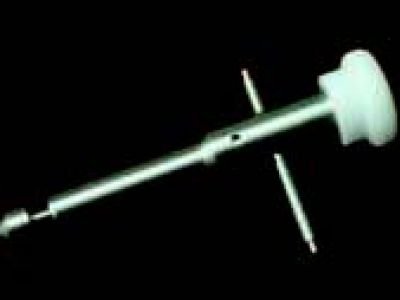
Plastic machining is more difficult than you would expect
The technology that is required to manufacture first class plastic components at a reasonable cost pushes the state of the art for machines, tools, and fixtures. For example, holding the plastic workpiece so it doesn’t flex during the machining process is somewhat of an art in itself.
Protomatic article “Plastic Prescription”
Cutting Tool Engineering magazine is highly focused for machinists and offers insight for developing new, competitive manufacturing methods.
This article featuring the manufacture of three plastic medical parts describes some of the industry solutions (and secrets) to machining these flexible materials.
Although, plastics are perceived to be easier to machine than aluminum, they are, in fact, more difficult since the thermal conductivity of plastic is lower than aluminum. Plastic typically has a coefficient of expansion 10 times that of metal.
This is important when optimizing the process since the cutting energy (heat from the material shearing process) must be transferred to the removed chip and not to the part. If the machining technique puts the heat energy into the part, the part will quickly expand out of tolerance, and then when the part cools, it will be smaller and possibly out of tolerance. This characteristic forces our Machinists to compensate for this contraction.
Our Machinists have developed proprietary methods for tolerance and finish control.
The second reason, is that plastic parts usually require smoother finishes for the final application. This part feature requires a smaller, very controlled cut per revolution to obtain the final finish.
Protomatic Machinists have applied state of the art cryogenic machining techniques at times to control the chip and finish formation.