Precision Machining
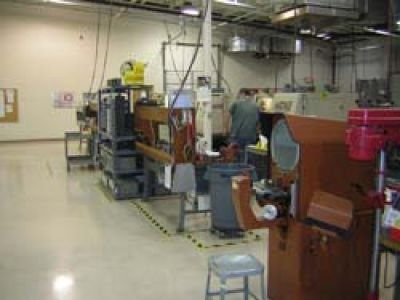
Milling machines are only as accurate as their operator and environment. There are many times when a machinist blames the machine tool when they are not getting the accuracy that the print demands. As the industry moves in a higher accuracy direction, engineers and manufacturers need to understand that there are many factors that are significant, complicated and often misunderstood when making high precision parts. This month we are highlighting some of the techniques that Protomatic uses to increase part accuracy.
Building Environment
Some materials are highly susceptible to their environment. The thermal coefficient of expansion can be a major factor with plastics and aluminum. Protomatic took this into account when designing and building our manufacturing environment. Our building has an excellent heating and cooling system that creates a uniform temperature during the day and night, and no skylights or sun faced windows in the manufacturing area, all of which creates a uniform environment for all seasons.
Precision Tool Holders
Tool holders are another important consideration. Minimizing tool run-out not only increases surface finish, but also increases tool positional performance as well as tool life. Low and ultra low run-out tool holders allow the tools to work as designed, with uniform cut on all cutting features. This decreases drill wander, making a straighter hole. The low run-out holders are naturally better balanced and also allows for higher cutting RPMs. The balance tool also increases the tool life due to minimized vibration during the critical cutting operations.
CNC Programming
Calculating the correct “chip load” for the tool and material combination is imperative. The experience of when to center drill, drill, bore, ream with controlled drill feed rate or peck drill cycles comes with experience. Many of machinists guess and guess close. This is the area of machinist magic (CAM and calculator) that is used to apply the correct operation cycle for material. This operation is critical for success. Confirmation is performed with acoustic measurement and analysis (software). We have both – the experienced machinists & software.
Coolant and Inserts
High quality tools and working with manufacturers that can support the product is important. Off brand manufacturers can provide cheap tools, but usually not the support and also have wider product variations. Understanding how to optimize is difficult enough without tool variations. Microscopically we look at the ground cutting edge to identify differences that are important to the application. Coolants are critical, most have great lubricity but you have to know what works for many applications. We use them all: liquid paraffin (wax), oils, semi-synthetics, Co2, Air (High pressure cold air) and Dry (no coolant).
Glass Scales
Machine tools that have glass scales also increase precision. All machines vary thermally and need to be warmed up to be stable. The thermal effect of the spindle motor, as well as warming of the lead screws affects positional location.
Monitor Variation
To monitor machine variation, the Renishaw Ball Bar (model WC20-W) should be used to confirm accuracy. We have used services or you can do it yourself. Either way, it is important to measure periodically. The knowledge of knowing that your machine repeats is critical.