Superalloys: A High-Strength, High-Performance Option
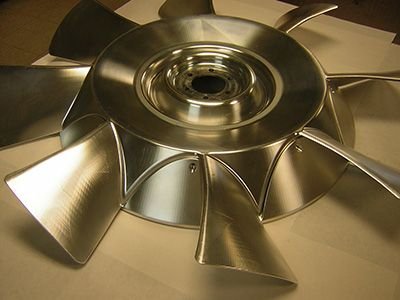
In this paper, you’ll learn the basics of high-performance superalloys, and be provided with some guidance for their use in new product applications and improved product design.
Superalloys are cobalt-, iron-, or nickel-based alloys. They are designed for high strength at elevated temperatures; creep properties; oxidation resistance; and corrosion resistance. The primary application for such alloys is in turbine engines, where creep is typically the lifetime-limiting factor in gas turbine blades.
Cobalt-based alloys are non-ferrous magnetic alloys with high strength and toughness, excellent corrosion and oxidation resistance, and high temperature strength. Cobalt’s properties result in its use for alloys in jet engine components, prosthetics, and magnets. Cobalt-based superalloys potentially possess superior hot-corrosion, oxidation, and wear resistance compared to Ni-based superalloys. But cobalt-based superalloys also typically have a lower strength at high temperatures than Ni-based superalloys. Additionally, cobalt-based alloys are the most expensive, with a current spot price for cobalt at $17.60/lb (October 2020), with a seven-year range fluctuating from $10.00 to $40.00/lb (2013-2020).
Cobalt Alloys
- FSX-414
- HS-1, HS-4, HS-6B, HS-12, HS-19, HS-21, HS-25, HS-31
- Haynes 188
- Jetalloy
- Mar M-302, M-509, M-905
- Ultimet
Iron-based alloys contain iron as the base metal. This category includes carbon steels, alloy steels, stainless steels, cast iron, maraging steel, and other specialty iron-based alloys with varying properties. Only a few of these alloys could be considered as superalloys. These are the least expensive alloy. Pricing is based not so much on iron content, but the other elements.
Iron-Based Alloys and Special
- Kovar
- Invar
- Nitronic 40, 50, 60
Nickel-based alloys are non-ferrous metals with high strength and toughness, excellent corrosion resistance, and superior elevated temperature properties. Nickel can also be magnetized. Nickel-based superalloys are the most common alloy class, resulting a wide range of applications including jet engine components, chemical process equipment, magnets, heating element components and electrical resistance elements. Nickel is also a useful alloying element in many other stainless, tool steels, maraging, and other alloy steels. Nickel-based alloys are the mid-priced superalloys, with a current spot price for nickel at $7.10/lb., and a seven-year range fluctuating from $4.00 to $10.00/lb. (2013-2020).
Nickel Alloys
- Inconel 600, 601, 617 625, 690
- Inconel 702, 713, 718, 722, 738, 750
- Inconel 800, 801, 825
- Inconel 901, 903
- Hastelloy B, B-2, C-4, C-22, C-276, C-2000, F, G, N, R, S, W, X
- Haynes 25, 36, 214, 230, 556
- HR-160, IN-100, MP35N, B-1900
- Mar M-002, M-200, M-246, M-247, M-421
- Monel 400, 405, 411, 500
- Mu Metal
- NichromeV
- Nickel 200
- Nim 101, 263
- Nimonic 75, 80A, 90
- Ni-Span 902
- Rene 41, 77, 80, 95, 125
- Supertherm
- Udimet 500, 520
- Waspaloy
Many superalloys are trademarked and use alternate names. Inconel™625 of Special Metals Corporation is also called Inco 625, Alloy 625, Nickel 625, Chornin® 625, Altemp® 625, Nickelvac® 625, Haynes® 625, Nicrofer® 6020; or is typically specified by American Military Standard (AMS) material designation. Many superalloys can be purchased in annealed and solution-heat-treated condition from the distributor or manufacturer.
For round bar/billet Inconel 625
AMS 5666 Condition A
Typical solution heat treatments are:
Solution 1950F and precipitation (age) hardened 1400F
Solution 2150F and precipitation (age) hardened 1200F
Inconel’s high temperature strength is developed by solid-solution strengthening or precipitation hardening, depending on the alloy.
Superalloys are the materials which have made very-high-temperature engineering technologies possible. But keep in mind, these alloys, like Inconel 625, are also very good for other applications.
Mild corrosive environments such as the atmosphere, fresh or salt water, neutral salts and alkaline environment have almost no attack.
In severe corrosive environments, the combination of nickel and chromium provides resistance to oxidizing chemicals, and molybdenum content supplies resistance to non-oxidizing environments. Further, elements such as niobium are stabilized for welding sensitization, thereby preventing intergranular cracking. This makes it one of the most highly utilized superalloys.
Finding the best alloy for an application is technically difficult, but there are resources to select the best for your application.
Protomatic Can Help
Protomatic is a CNC machine shop specializing in prototype and short-run CNC parts. From aerospace parts machining to medical device machining, everything is designed and made with Life-Saving Precision.
Protomatic works with many superalloys. If you are interested in developing a new product, upgrading a current product, or contract manufacturing, please contact us for more information. If a prototype is needed, please call for a quote request.
About the author: Doug Wetzel is Vice President and General Manager of Protomatic. Protomatic is a CNC precision machining shop specializing in prototype and short-run production components for the medical, aerospace and other technical industries. Because of the critical nature of the parts they design and manufacture, the emphasis is always on Life-Saving Precision.