Why Bring Manufacturing Back to America?
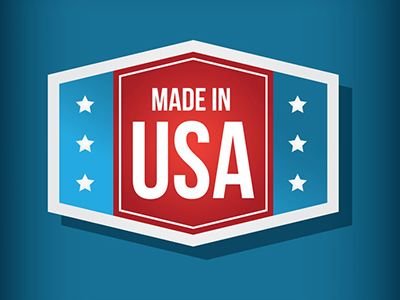
American manufacturers periodically need to reevaluate their offshoring practices and consider reshoring products to America. Companies are increasingly recognizing that previously ignored risks, strategic impacts and costs are becoming significant. Many are becoming exposed to a high-risk environment where market wage advantages are not sufficient protection. Manufacturers are now seeing the benefits of proximity, producing in the market, and evaluating the total cost of doing business.
Businesses are all different due to their labor content, material content and regulatory requirements. However, there are some things they all share in common. Following are some important topics companies should consider when comparing offshoring vs. reshoring.
The best product quality
- Quality consistency – This is hard to benchmark, but easy to measure after selecting a supplier. When evaluating suppliers prior to manufacturing, infrastructure technology and track record are typically the best ways to measure expected product quality. The USA has a history of producing the highest quality materials.
- Skilled workforce – The United States has a highly skilled and experienced base of workers. In addition, record trade school enrollments prove that American workers are eager to learn and advance their careers.
- Communication to resolve/understand issues – English is the technical language of the world and the primary language in the United States. English helps speed day-to-day business by making it easier to resolve and understand complex products and systems.
The shortest lead time
- Shorter and more consistent – Offshore supply chains are complex and complicated. By locating manufacturing closer, products can be ready for distribution sooner. This requires less overall inventory and increases the ability to improve products quicker.
- Lower inventory levels – Minimizing inventory is a major task for many companies. Complex product pipelines add to the overall cost.
- Cost of Freight – Energy costs typically are trending upward, making air freight even more expensive. Alternative means of shipping instead of air can add as much as six weeks to the lead time.
- Communication – Simple communications, such as for an order and acknowledgement of delivery, should go quickly. Test email, phone, or other methods to determine which works best for you and your suppliers.
The lowest short-term and long-term cost
- Rising offshore wages – Trends show a global 7-8% annual wage increase, while USA wages are stagnant. In the long term, global wages will be more on balance with those here as the cost of living in developing countries is raised.
- Ease of Communication – Communication is singly the most important factor in product cost. Languages and time zones are minor barriers to great communication. The true test is effective responsiveness to change. Some issues can be resolved with corporate culture. But if the message is not understood, the issue will not be fixed.
- Import/export tariff present – The United States is changing tariff policies. Terms may need adjustment and customer pricing changed. Customers are sensitive to significant price changes, so product sales may be affected.
- Infrastructure (consistent) – The lowest cost is not everything. A company that requires electricity is far less effective when it is not available 24/7. Water, electricity, employee housing and employee transportation all affect product cost. In China, energy costs have continued to rise by 15% annually since 2010. Real estate is also a growing concern for housing, factory space and increased distance to vital transportation hubs.
The best regulatory environment
- Cost requirements – Local tax incentives may come into play. Also consider the cost of paying for special licenses and unethical behavior in the form of graft.
- Intellectual property – This is a chronic issue in offshoring that threatens production and design. Reshoring in the USA provides better protection for IP and non-disclosure agreements.
- Regulatory compliance issues – These are unique to each industry and country, and some are significant. Fewer problems arise when manufacturing is done in-country, especially with perishables and medical.
- Improved innovation and product differentiation – Loss of Intellectual Property and product improvement requires honest and open feedback.
Why Reshoring Makes Sense for America
Reshoring is the fastest and most efficient way to strengthen the U.S. economy because it:
- Helps balance the trade and budget deficits
- Reduces unemployment by creating productive jobs
- Reduces income inequality
- Motivates skilled workforce recruitment by demonstrating that manufacturing is a growth career
- Helps maintain the broad industrial capability required for national defense
- Broad industrial capability creates improved infrastructure, driving down costs
- Increases sense of patriotism with employees
Bottom line? The grass isn’t always greener on the overseas side. More often than not, reshoring right here in our own backyard is a smarter way to go.
About the author: Doug Wetzel is Vice President and General Manager of Protomatic. Protomatic is a CNC precision machining shop specializing in prototype and short-run production components for the medical, aerospace and other technical industries. Because of the critical nature of the parts they design and manufacture, the emphasis is always on Life-Saving Precision.